POM部品の耐久性を高めるための加工方法とは?
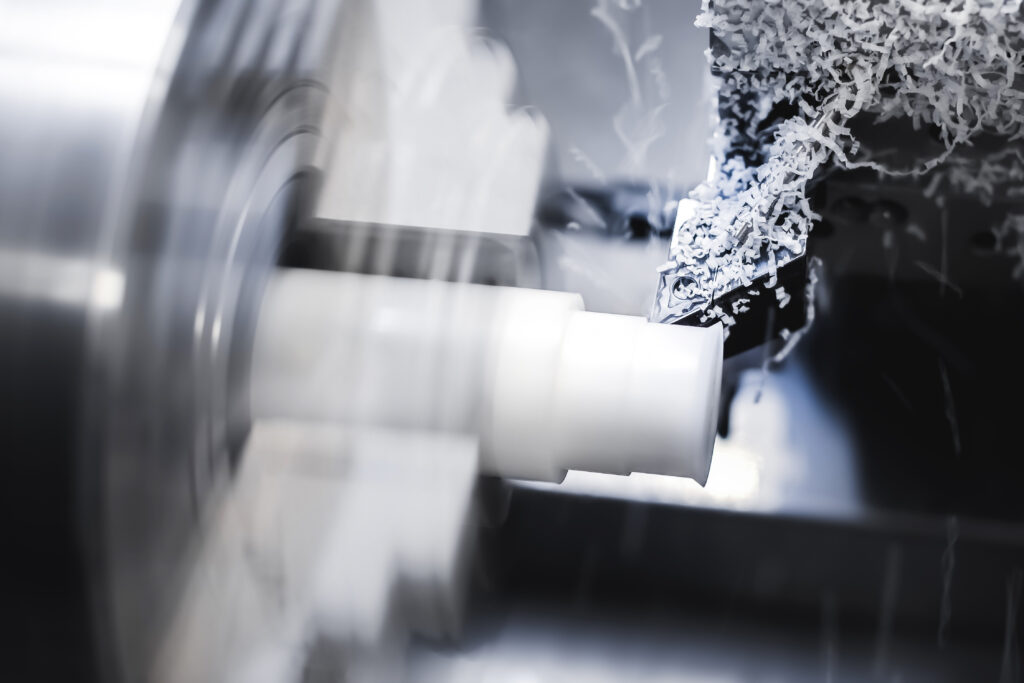
あなたは「POM部品の耐久性を向上させたいが、具体的に何をすればいいのか分からない」とお悩みですか?そんな方のために、私たちは「POM部品の耐久性を高めるための加工方法」に関する完全ガイドを作成しました。
この記事は、次のような疑問を抱いている方々に向けています。
- POM部品とは何か、その特性は?
- POM部品の耐久性を向上させる具体的な加工方法は?
- 加工方法を実施するためのステップやポイントは?
POM(ポリアセタール)は、その優れた機械的特性や耐摩耗性から、多くの産業で利用されていますが、耐久性を向上させるためには適切な加工が必須です。この記事では、POM部品の特性を理解し、耐久性を高めるための様々な加工方法について詳しく解説します。これを読めば、あなたのPOM部品がどのようにしてより長持ちするのか、その秘密が明らかになります。ぜひ最後までお付き合いください。
1. POM部品の耐久性と加工方法の基礎知識
1-1. POM樹脂の特性
POM(ポリアセタール)は、耐摩耗性、耐衝撃性、耐薬品性に優れたエンジニアリングプラスチックの一つです。その結晶性の高い構造により、剛性と強度が高く、長期間の使用でも安定した性能を発揮します。また、自己潤滑性を持つため、摩擦による劣化を抑制し、潤滑剤なしでの使用も可能です。加工性も良く、射出成形や切削加工が容易で、多種多様な部品製作に適しています。
1-2. POM部品の一般的な用途
POMはその高い耐久性と機械的特性を活かし、自動車部品(ギア、ベアリング、シールリングなど)、家電製品の可動部品、産業機械の精密部品、医療機器の構造部品など幅広い分野で活用されています。特に摩擦や衝撃が頻繁に発生する箇所でその真価を発揮し、製品の寿命延長に大きく寄与しています。
2. POM部品の耐衝撃性を向上させる加工方法
2-1. 耐衝撃性向上のための材料選定
耐衝撃性を高めるには、POMの中でも特に衝撃強度に優れたグレードを選ぶことが重要です。例えば、共重合体タイプのPOMは、均一な分子構造によって割れにくく、耐衝撃性が高い傾向にあります。用途に応じて添加剤を配合した改良材も選択され、衝撃負荷に強い部品製作が可能となります。
2-2. 加工技術の選択肢
加工方法としては、射出成形が主流ですが、切削加工や機械加工も用いられます。耐衝撃性を損なわないためには、加工時の熱の発生や応力集中を避けることがポイントです。冷却条件の最適化や切削速度の調整を行うことで、部品内部のひずみや割れを防止できます。
2-3. 実際の加工事例
例えば、自動車のギア部品製作においては、適切な冷却設計と射出速度管理により、内部応力の発生を抑えつつ高精度な部品成形が実現されています。これにより、耐衝撃性の向上だけでなく、寸法安定性も確保され、耐久性の高い製品が量産されています。
3. POM部品の耐摩耗性を最大限に引き出す加工技術
3-1. 耐摩耗性を高めるための表面処理
POMの耐摩耗性はもともと高いですが、さらに表面を硬化させるために特殊な表面処理が行われることがあります。例えば、フッ素コーティングやプラズマ処理により、摩擦抵抗を減少させるとともに、表面の耐久性を強化できます。こうした処理は、摩擦頻度が高い機械部品に特に効果的です。
3-2. 加工条件の最適化
耐摩耗性向上のためには、加工時の熱影響を最小限に抑えることが重要です。過剰な熱は結晶構造の劣化や応力発生の原因となり、摩耗を促進します。そのため、射出成形では金型温度の管理や射出圧力の調整を行い、切削加工では適切な切削速度とクーラントの使用を徹底します。
3-3. 耐摩耗性向上の成功事例
産業機械の軸受部品にPOMを用いたケースでは、適切な表面処理と加工管理により摩耗速度が大幅に低減されました。結果としてメンテナンス間隔が延長し、設備の稼働率向上に貢献しています。このような成功事例は、POMの耐摩耗性を最大限に活かすための加工技術の重要性を示しています。
4. POM樹脂加工における注意点と失敗を避けるための情報
4-1. 加工時の注意点
POM樹脂を加工する際は、熱による変形や内部応力の蓄積を防ぐことが重要です。加工温度が高すぎると材料の劣化や寸法の狂いが発生しやすいため、射出成形では金型温度や射出速度の管理が不可欠です。また、切削加工では工具の刃先の摩耗を避けるために適切な切削速度や切削条件を選定し、冷却剤を十分に用いることが求められます。さらに、POMは吸湿性が低いものの、加工前に十分に乾燥させることで加工精度が向上します。
4-2. よくある失敗とその対策
POM加工でよく見られる失敗には、成形品の割れやひび割れ、寸法不良、表面のざらつきなどがあります。これらは過剰な加工熱や冷却不足、金型設計の不備が原因で起こることが多いです。対策としては、冷却回路の最適化や射出圧力の適正化、加工環境の一定化が効果的です。また、切削加工では工具の摩耗や刃先の欠けに注意し、定期的なメンテナンスと工具交換が推奨されます。
4-3. 成功するためのヒント
POM加工で成功を収めるためには、材料の特性を深く理解した上で加工条件を細かく調整することが鍵です。特に、熱管理と応力除去の工夫は不可欠です。さらに、試作段階で多様な加工パラメータを検証し、最適な条件を見つけることが製品品質の安定につながります。加えて、適切な乾燥や保管環境の確保も長期的な品質維持には欠かせません。
5. POMとPEEKの性質の違いと加工ポイントの比較
5-1. POMとPEEKの基本的な特性の違い
POMは高い剛性と耐摩耗性を持ち、優れた自己潤滑性で多くの産業用途に適しています。一方、PEEK(ポリエーテルエーテルケトン)はさらに高温耐性や化学耐性に優れ、250℃以上の高温環境でも性能を維持できる特性を持ちます。PEEKは高価ですが、その耐熱性や耐薬品性から航空宇宙や医療分野で重宝されています。
5-2. 加工方法の違い
POMは射出成形や切削加工が比較的容易で、生産コストも抑えられますが、加工時の温度管理には注意が必要です。PEEKは高温加工が必要なため、専用の射出成形設備や高耐熱工具が求められます。また、切削加工も高度な技術が必要で、冷却や切削速度の最適化が不可欠です。PEEKの加工には熟練度が要求されるため、加工工程の計画が重要です。
5-3. 用途に応じた選択基準
製品の使用環境や要求される性能に応じて材料を選定します。耐摩耗性や加工のしやすさを重視する場合はPOMが適していますが、高温環境や厳しい化学耐性が必要な場合はPEEKが選ばれます。コスト面も考慮しながら、製品の長期的な性能や安全性を考えた材料選択が重要です。用途例として、自動車の一般部品にはPOMが多用される一方で、航空機の高温耐性部品にはPEEKが使われる傾向があります。
まとめ
POM部品の耐久性を高めるためには、表面処理や熱処理、充填剤の添加が効果的です。表面処理により摩耗や腐食に強くなり、熱処理で強度を向上させます。また、充填剤を加えることで機械的特性を改善し、全体的な性能を向上させることができます。これらの方法を組み合わせることで、POM部品の長寿命化が図れます。